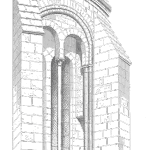
testes não destrutivos de soldas. Processos e métodos de soldagem podem introduzir contaminantes e defeitos metalúrgicos na solda. Se uma solda for necessária para suportar condições de carga severas e tensões, é fundamental garantir que sua qualidade atenda aos padrões mínimos. As soldas podem ser testadas por técnicas destrutivas e não destrutivas. A maior parte da produção é testada pelo uso de métodos não destrutivos. Os testes não destrutivos mais comuns para verificar soldas são inspeção Visual, Líquido Penetrante, Partícula Magnética, corrente parasita, Ultra-Som, Emissão acústica e radiografia. Palavras-chave: NDT, controle de qualidade, não conformidade, Verificação, procedimento de solda.
quando o metal é soldado, a poça derretida esfria e solidifica. Durante o resfriamento, a qualidade da solda pode ser comprometida por inclusões como escória, por erro humano de fadiga, por configuração e técnica erradas, por erro de equipamento devido a avarias, por efeitos ambientais, como baixa temperatura e umidade, e por fenômeno metalúrgico de Metais incompatíveis ou altas taxas de resfriamento. Como a soldagem é altamente dependente de fatores controlados por humanos, talvez seja necessário provar que a qualidade do trabalho é adequada para o dever.
em todos os métodos de NDT descritos abaixo, a certeza da conformidade depende inteiramente da capacidade do inspetor. Resultados de alta qualidade só são possíveis de pessoas treinadas, competentes e experientes. Não use pessoas não qualificadas para fazer qualquer um dos testes que você está prestes a ler.
inspeção Visual
este método usa um observador qualificado e treinado observando a solda enquanto o soldador está funcionando. O observador observa a piscina de solda e o metal de resfriamento. Eles normalmente procuram inclusões, subcotação (a altura da solda está abaixo da altura do metal pai), profundidade de penetração da solda e certeza de ligação ao metal pai.
quando um defeito não conforme é observado, o ponto é marcado. No final da solda, o defeito é moído e a solda é refeita com a qualidade necessária.
inspeção de líquido ou corante penetrante
como o nome sugere, um agente corante é usado para detectar defeitos de solda. Este método só encontrará rachaduras na superfície e descontinuidades na superfície. A superfície de solda é completamente limpa de incrustações e respingos (mas não disparada, pois fechará sobre os defeitos). Uma lavagem com detergente é usada para remover a sujeira, uma pasta de decapagem é usada para remover tinta ou graxa e um desengordurante ou solvente é aplicado para remover o óleo. Apenas uma superfície metálica limpa é aceitável.
o sistema normalmente vem em duas latas de spray-uma é penetrante e a outra é desenvolvedora. O penetrante é pulverizado sobre a solda e a ação capilar Desenha-a em quaisquer rachaduras mínimas na superfície. O penetrante na superfície é limpo e o penetrante nas rachaduras permanece molhado. Após um curto período de tempo, o desenvolvedor é pulverizado sobre a solda. O desenvolvedor atua para extrair o corante penetrante das rachaduras e, portanto, muda de cor. Ele se comporta como papel absorvente e amplia a presença da rachadura.
Inspeção De Partículas Magnéticas
este método usa mudanças em um campo magnético para detectar descontinuidades de superfície e logo abaixo da superfície. Quando um campo magnético é interrompido por um defeito, o campo se distorce em torno do defeito. As limalhas magnéticas pulverizadas colocadas no campo podem mostrar esta distorção. Este método é utilizável apenas para metais ferro-magnéticos (magnéticos à base de ferro).
quando usado para testar soldas, o campo magnético é produzido colocando prods de metal em cada lado da solda e introduzindo uma baixa corrente elétrica através do metal ou colocando a peça de metal em um campo magnético. Os campos magnéticos são induzidos na parte pelo campo magnético externo.
uma vez que o campo magnético é estabelecido, algumas partículas de metal coloridas em pó são colocadas na peça. O padrão criado pelo pó no campo magnético é inspecionado quanto a distorções de campo. As partículas podem ser usadas molhadas (em suspensão de querosene) ou secas dependendo da localização das peças e da finalidade do exame.
inspeção de corrente parasita
o princípio de operação é a detecção de fluxo de corrente elétrica alterado em uma bobina de fio elétrico. O fluxo de corrente elétrica alternada através de uma bobina cria um campo magnético flutuante ao redor da bobina. Se o campo magnético é trazido para perto da condução de metal, correntes elétricas parasitas se desenvolvem no metal. As correntes parasitas, por sua vez, montaram um campo magnético em oposição ao campo primário da bobina.
todas as flutuações no campo magnético secundário devido a distorções também alterar a força do campo principal, que por sua vez altera o fluxo de corrente elétrica através da bobina primária. A mudança no fluxo de corrente da bobina primária é detectada. A quantidade da mudança atual representa o efeito de uma descontinuidade causando a distorção no campo secundário.
este método é usado para detectar defeitos de solda profundamente no metal. Profundidades de até 25 mm são possíveis dependendo do metal que está sendo testado e da velocidade com que a corrente alternada muda (sua frequência).
esta é a abordagem preferida para testar pisos e paredes de tanques de aço. Um scanner de rastreamento é enviado pela superfície e as alterações na corrente parasita são mostradas em uma tela de monitoramento. Onde a evidência de uma descontinuidade é encontrada, o local é marcado e, em seguida, um exame local mais completo é realizado com outro equipamento de NDT para quantificar o defeito.
inspeção ultrassônica
ondas sonoras de alta frequência são enviadas para um metal usando uma sonda emissora. Se as ondas encontrarem uma descontinuidade, elas saltam e retornam à sonda onde são detectadas. O tamanho e a localização da descontinuidade são exibidos em uma tela de monitoramento.
o método não pode ser usado para falhas superficiais e próximas à superfície. Uma zona morta ocorre logo abaixo do ponto de contato da sonda. Para assegurar a conexão acústica apropriada entre a ponta de prova e a superfície do metal um agente líquido do acoplamento, como a graxa, é usado entre os dois. A superfície do teste é exigida para ser lisa bastante para que o agente do acoplamento mantenha o contato entre a ponta de prova e o metal. Onde a solda é muito alta, é necessária uma técnica diferente que use o som refletido para verificar se há descontinuidades.
os tamanhos dos defeitos que podem ser detectados dependem do comprimento de onda do som. Por via de regra o defeito tem que ser metade do comprimento de onda para ser detectável. Metais diferentes têm comprimentos de onda diferentes para a mesma frequência sonora. Em aço a 2 MHz, defeitos de 1,5 mm são detectáveis.
monitoramento de emissões acústicas
as emissões acústicas são ondas de estresse produzidas por movimentos bruscos em materiais estressados. Quando um material é colocado sob carga, ele se deforma um pouco. Os movimentos internos produzidos pela deformação criam sons que viajam pela estrutura. Esses sons podem ser detectados e a fonte do movimento localizada. Uma vez encontrada a fonte, outras técnicas de NDT são usadas para quantificar o movimento e qualquer presença de descontinuidades.
este método é frequentemente usado em grandes estruturas existentes, como tanques e vasos de pressão, pois é rápido e de baixo custo. Sensores fixos estão localizados na estrutura e normalmente colocados a cada 1 a 6 metros de distância. A estrutura é “carregada” na forma ascendente, passo-a-passo e as emissões acústicas gravadas em um monitor de exibição. O carregamento é variado ou mantido constante por um período de tempo e as mudanças nas emissões acústicas indicam se a estrutura continua a se mover internamente.
por fatoração – na velocidade do som do metal, o ponto de emissão pode ser localizado por triangulação com boa precisão. O ruído de fundo pode interferir nos resultados. Esse problema pode ser superado parando o ruído em sua fonte, filtrando-o usando a eletrônica dentro do equipamento de monitoramento ou usando uma frequência de medição diferente da frequência de ruído.
Radiografia Industrial
a inspeção radiográfica é baseada na absorção de radiação por materiais de diferentes densidades. Na indústria de engenharia, raios-X ou raios gama são usados. É um processo caro, mas penetra quase todos os materiais em grandes profundidades.
a fonte de radiação é colocada em um lado da solda que está sendo testada e a película “fotográfica” de detecção é colocada do outro lado da solda. À medida que a radiação passa pelas descontinuidades da solda, atuam como redutores de densidade, permitindo mais radiação através deles. O alto nível de radiação aparece como uma cor mais escura no filme.
como a imagem criada no filme é uma ‘sombra’, ela pode ser afetada por fatores como alterações na espessura do sujeito, dispersão de radiação, fatores geométricos que influenciam a radiação, posicionamento da fonte, tempos de exposição e qualidade do filme.
Mike Sondalini – Engenheiro De Longevidade De Equipamentos