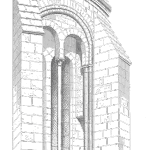
Contrôle non destructif des soudures. Les procédés et méthodes de soudage peuvent introduire des contaminants et des défauts métallurgiques dans la soudure. Si une soudure est nécessaire pour résister à des conditions de charge et à des contraintes sévères, il est essentiel de s’assurer que sa qualité répond aux normes minimales. Les soudures peuvent être testées par des techniques destructives et non destructives. La plupart de la production est testée par l’utilisation de méthodes non destructives. Les tests non destructifs les plus courants pour vérifier les soudures sont l’Inspection visuelle, le Ressuage liquide, les Particules Magnétiques, les Courants de Foucault, les Ultrasons, l’Émission Acoustique et la Radiographie. Mots-clés : CND, contrôle qualité, non-conformité, vérification, procédure de soudure.
Lorsque le métal est soudé, la flaque d’eau fondue se refroidit et se solidifie. Pendant le refroidissement, la qualité de la soudure peut être compromise par des inclusions telles que des scories, par une erreur humaine due à la fatigue, par une configuration et une technique incorrectes, par une erreur d’équipement due à des pannes, par des effets environnementaux tels que la basse température et l’humidité, et par un phénomène métallurgique provenant de métaux incompatibles ou de vitesses de refroidissement élevées. Parce que le soudage dépend fortement de facteurs contrôlés par l’homme, il est peut-être nécessaire de prouver que la qualité du travail est appropriée pour le devoir.
Dans toutes les méthodes de CND décrites ci-dessous, la certitude de la conformité dépend entièrement de la capacité de l’inspecteur. Des résultats de haute qualité ne sont possibles que par des personnes formées, compétentes et expérimentées. N’utilisez pas de personnes non qualifiées pour faire l’un des tests que vous êtes sur le point de lire.
Inspection visuelle
Cette méthode utilise un observateur qualifié et formé qui surveille la soudure pendant que le soudeur travaille. L’observateur surveille le bain de soudure et le métal de refroidissement. Ils recherchent généralement les inclusions, la sous-découpe (la hauteur de soudure est inférieure à la hauteur du métal parent), la profondeur de pénétration de la soudure et la certitude de la liaison au métal parent.
Lorsqu’un défaut non conforme est observé, le point est marqué. À la fin de la soudure, le défaut est rectifié et la soudure est refaite à la qualité requise.
Inspection par ressuage de liquide ou de colorant
Comme son nom l’indique, un colorant est utilisé pour détecter les défauts de soudure. Cette méthode ne détectera que les fissures de surface et les discontinuités de surface. La surface de soudure est soigneusement nettoyée du tartre et des éclaboussures (mais pas grenaillée car elle se refermera sur les défauts). Un lavage au détergent est utilisé pour enlever la saleté, une pâte de décapage est utilisée pour enlever la peinture ou la graisse et un dégraissant ou un solvant est appliqué pour éliminer l’huile. Seule une surface métallique propre est acceptable.
Le système se présente normalement en deux boîtes de pulvérisation – l’une est le pénétrant et l’autre est le révélateur. Le pénétrant est pulvérisé sur la soudure et l’action capillaire l’entraîne dans des fissures superficielles minuscules. Le pénétrant sur la surface est essuyé et le pénétrant dans les fissures reste humide. Après un court temps d’arrêt, le révélateur est pulvérisé sur la soudure. Le révélateur agit pour extraire le colorant pénétrant des fissures et change ainsi de couleur. Il se comporte comme du papier buvard et magnifie la présence de la fissure.
Inspection des particules magnétiques
Cette méthode utilise les changements dans un champ magnétique pour détecter les discontinuités de surface et juste en dessous de la surface. Lorsqu’un champ magnétique est interrompu par un défaut, le champ se déforme autour du défaut. Les limailles magnétiques en poudre placées dans le champ peuvent montrer cette distorsion. Cette méthode n’est utilisable que pour les métaux ferromagnétiques (magnétiques à base de fer).
Lorsqu’il est utilisé pour tester les soudures, le champ magnétique est produit soit en plaçant des protubérances métalliques de chaque côté de la soudure et en introduisant un faible courant électrique à travers le métal, soit en plaçant la pièce métallique dans un champ magnétique. Les champs magnétiques sont induits dans la pièce par le champ magnétique externe.
Une fois le champ magnétique établi, quelques particules métalliques poudrées et colorées sont placées sur la pièce. Le motif créé par la poudre dans le champ magnétique est inspecté pour détecter les distorsions de champ. Les particules peuvent être utilisées humides (dans une suspension de kérosène) ou sèches selon l’emplacement des pièces et le but de l’examen.
Inspection par courants de Foucault
Le principe de fonctionnement est la détection du flux de courant électrique modifié dans une bobine de fil électrique. Le flux de courant électrique alternatif à travers une bobine crée un champ magnétique fluctuant autour de la bobine. Si le champ magnétique est rapproché du métal conducteur, des courants électriques de foucault se développent dans le métal. Les courants de Foucault créent à leur tour un champ magnétique en opposition au champ primaire de la bobine.
Toute fluctuation du champ magnétique secondaire due à des distorsions modifie également l’intensité du champ primaire, qui à son tour modifie le flux de courant électrique à travers la bobine primaire. Le changement du flux de courant de la bobine primaire est détecté. La quantité de changement de courant représente l’effet d’une discontinuité provoquant la distorsion dans le champ secondaire.
Cette méthode est utilisée pour détecter les défauts de soudure profondément dans le métal. Des profondeurs allant jusqu’à 25 mm sont possibles en fonction du métal testé et de la vitesse à laquelle le courant alternatif change (sa fréquence).
C’est l’approche privilégiée pour tester les sols et les murs des réservoirs en acier. Un scanner rampant est envoyé à travers la surface et les changements dans le courant de Foucault sont affichés sur un écran de surveillance. Lorsque des signes de discontinuité sont constatés, la tache est marquée, puis un examen local plus approfondi est effectué avec d’autres équipements CND pour quantifier le défaut.
Inspection par ultrasons
Des ondes sonores à haute fréquence sont envoyées dans un métal à l’aide d’une sonde émettrice. Si les ondes rencontrent une discontinuité, elles rebondissent et retournent à la sonde où elles sont détectées. La taille et l’emplacement de la discontinuité sont affichés sur un écran de surveillance.
La méthode ne peut pas être utilisée pour les défauts de surface et proches de la surface. Une zone morte se produit juste en dessous du point de contact de la sonde. Pour assurer une bonne connexion acoustique entre la sonde et la surface métallique, un agent de couplage liquide, comme de la graisse, est utilisé entre les deux. La surface d’essai doit être suffisamment lisse pour que l’agent de couplage maintienne le contact entre la sonde et le métal. Lorsque la soudure est trop haute, une technique différente est requise qui utilise le son réfléchi pour vérifier les discontinuités.
La taille des défauts pouvant être détectés dépend de la longueur d’onde du son. En règle générale, le défaut doit être la moitié de la longueur d’onde pour être détectable. Différents métaux ont des longueurs d’onde différentes pour la même fréquence sonore. Dans l’acier à 2 MHz, des défauts de 1,5 mm sont détectables.
Surveillance des émissions acoustiques
Les émissions acoustiques sont des ondes de contrainte produites par un mouvement soudain dans des matériaux soumis à des contraintes. Lorsqu’un matériau est placé sous charge, il se déforme très légèrement. Les mouvements internes produits par la déformation créent des sons qui traversent la structure. Ces sons peuvent être détectés et la source du mouvement localisée. Une fois la source trouvée, d’autres techniques de CND sont utilisées pour quantifier le mouvement et toute présence de discontinuités.
Cette méthode est souvent utilisée sur les grandes structures existantes, telles que les réservoirs et les récipients sous pression, car elle est rapide et peu coûteuse. Des capteurs fixes sont situés sur la structure et généralement placés tous les 1 à 6 mètres de distance. La structure est « chargée » de manière ascendante et progressive et les émissions acoustiques enregistrées sur un écran d’affichage. La charge est modifiée ou maintenue constante pendant un certain temps et les changements d’émissions acoustiques indiquent si la structure continue de se déplacer intérieurement.
Par factorisation – dans la vitesse du son du métal, le point d’émission peut être localisé par triangulation avec une bonne précision. Le bruit de fond peut interférer avec les résultats. Ce problème peut être résolu en arrêtant le bruit à sa source, en le filtrant à l’aide de l’électronique de l’équipement de surveillance ou en utilisant une fréquence de mesure différente de la fréquence du bruit.
Radiographie industrielle
L’inspection radiographique est basée sur l’absorption du rayonnement par des matériaux de densité différente. Dans l’industrie de l’ingénierie, des rayons X ou des rayons gamma sont utilisés. C’est un procédé coûteux mais qui pénètre presque tous les matériaux à de grandes profondeurs.
La source de rayonnement est placée d’un côté de la soudure à tester et le film « photographique » de détection est placé de l’autre côté de la soudure. Lorsque le rayonnement traverse les discontinuités de soudure, elles agissent comme des réducteurs de densité permettant plus de rayonnement à travers elles. Le niveau élevé de rayonnement apparaît sous la forme d’une couleur plus foncée sur le film.
Comme l’image créée sur le film est une « ombre », elle peut être affectée par des facteurs tels que les changements d’épaisseur du sujet, la diffusion du rayonnement, les facteurs géométriques influençant le rayonnement, le positionnement de la source, les temps d’exposition et la qualité du film.
Mike Sondalini – Ingénieur Longévité des équipements