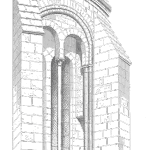
Ensayos no destructivos de soldaduras. Los procesos y métodos de soldadura pueden introducir contaminantes y defectos metalúrgicos en la soldadura. Si se requiere una soldadura para soportar condiciones de carga y tensiones severas, es fundamental asegurar que su calidad cumpla con los estándares mínimos. Las soldaduras se pueden probar con técnicas destructivas y no destructivas. La mayor parte de la producción se prueba mediante el uso de métodos no destructivos. Las pruebas no destructivas más comunes para verificar soldaduras son Inspección Visual, Penetrante de Líquido, Partículas Magnéticas, Corrientes de Foucault, Ultrasonidos, Emisión Acústica y Radiografía. Palabras clave: END, control de calidad, no conformidad, verificación, procedimiento de soldadura.
Cuando se suelda el metal, el charco fundido se enfría y solidifica. Durante el enfriamiento, la calidad de la soldadura puede verse comprometida por inclusiones como escoria, por error humano por fatiga, por configuración y técnica incorrectas, por error de equipo debido a averías, por efectos ambientales como baja temperatura y humedad, y por fenómeno metalúrgico de metales incompatibles o altas tasas de enfriamiento. Debido a que la soldadura depende en gran medida de factores controlados por humanos, tal vez sea necesario demostrar que la calidad del trabajo es adecuada para el deber.
En todos los métodos de ensayos no destructivos descritos a continuación, la certeza del cumplimiento depende totalmente de la capacidad del inspector. Los resultados de alta calidad solo son posibles de personas capacitadas, competentes y experimentadas. No utilice personas no calificadas para hacer ninguna de las pruebas que está a punto de leer.
Inspección visual
Este método utiliza un observador calificado y entrenado que observa la soldadura mientras el soldador está trabajando. El observador observa la piscina de soldadura y el metal de enfriamiento. Por lo general, buscan inclusiones, socavación (la altura de soldadura está por debajo de la altura del metal original), profundidad de penetración de la soldadura y certeza de la unión al metal original.
Cuando se observa un defecto no conforme, se marca el lugar. Al final de la soldadura ejecutar el defecto es de tierra y la soldadura se rehizo a la calidad requerida.
Inspección de líquidos o colorantes Penetrantes
Como su nombre indica, se utiliza un agente colorante para detectar defectos de soldadura. Este método solo encontrará grietas superficiales y discontinuidades superficiales. La superficie de soldadura se limpia a fondo de incrustaciones y salpicaduras (pero no de granallado, ya que se cerrará sobre los defectos). Se usa un detergente para eliminar la suciedad, se usa una pasta de decapado para eliminar la pintura o la grasa y se aplica un desengrasante o disolvente para eliminar el aceite. Solo se acepta una superficie metálica limpia.
El sistema normalmente viene en dos latas de aerosol, una es el penetrante y la otra es el revelador. El penetrante se rocía sobre la soldadura y la acción capilar lo introduce en grietas superficiales de cualquier minuto. El penetrante en la superficie se limpia y el penetrante en las grietas permanece húmedo. Después de un corto tiempo de permanencia, el revelador se pulveriza sobre la soldadura. El revelador actúa para extraer el tinte penetrante de las grietas y, por lo tanto, cambia de color. Se comporta como papel secante y aumenta la presencia de la grieta.
Inspección de partículas magnéticas
Este método utiliza cambios en un campo magnético para detectar discontinuidades superficiales y justo debajo de la superficie. Cuando un defecto interrumpe un campo magnético, el campo se distorsiona alrededor del defecto. Las limaduras magnéticas en polvo colocadas en el campo pueden mostrar esta distorsión. Este método solo se puede utilizar para metales ferromagnéticos (magnéticos a base de hierro).
Cuando se utiliza para probar soldaduras, el campo magnético se produce colocando clavos metálicos a cada lado de la soldadura e introduciendo una baja corriente eléctrica a través del metal o colocando la pieza metálica en un campo magnético. Los campos magnéticos son inducidos en la pieza por el campo magnético externo.
Una vez establecido el campo magnético, se colocan en la pieza unas cuantas partículas metálicas coloreadas en polvo. El patrón creado por el polvo en el campo magnético se inspecciona para detectar distorsiones de campo. Las partículas se pueden utilizar húmedas (en una suspensión de queroseno) o secas, según la ubicación de las piezas y el propósito del examen.
Inspección de corriente de Foucault
El principio de funcionamiento es la detección de flujo de corriente eléctrica cambiado en una bobina de cable eléctrico. El flujo de corriente eléctrica alterna a través de una bobina crea un campo magnético fluctuante alrededor de la bobina. Si el campo magnético se acerca al metal conductor, se desarrollan corrientes eléctricas de foucault en el metal. Las corrientes de foucault a su vez establecen un campo magnético en oposición al campo primario de la bobina.
Cualquier fluctuación en el campo magnético secundario debido a distorsiones también cambia la fuerza del campo primario, que a su vez cambia el flujo de corriente eléctrica a través de la bobina primaria. Se detecta el cambio en el flujo de corriente de la bobina primaria. La cantidad del cambio actual representa el efecto de una discontinuidad que causa la distorsión en el campo secundario.
Este método se utiliza para detectar defectos de soldadura profundamente en el metal. Son posibles profundidades de hasta 25 mm en función del metal que se está probando y de la velocidad a la que cambia la corriente alterna (su frecuencia).
Este es el enfoque preferido para probar pisos y paredes de tanques de acero. Se envía un escáner de rastreo a través de la superficie y los cambios en la corriente de foucault se muestran en una pantalla de monitoreo. Cuando se encuentra evidencia de una discontinuidad, se marca el lugar y luego se realiza un examen local más exhaustivo con otros equipos de END para cuantificar el defecto.
Inspección ultrasónica
Las ondas sonoras de alta frecuencia se envían a un metal mediante una sonda emisora. Si las ondas encuentran una discontinuidad, rebotan en ella y regresan a la sonda donde se detectan. El tamaño y la ubicación de la discontinuidad se muestran en una pantalla de monitoreo.
El método no se puede utilizar para fallas superficiales y cercanas a la superficie. Una zona muerta se produce justo debajo del punto de contacto de la sonda. Para asegurar una conexión acústica adecuada entre la sonda y la superficie metálica, se utiliza un agente de acoplamiento líquido, como grasa, entre los dos. Se requiere que la superficie de ensayo sea lo suficientemente lisa para que el agente de acoplamiento mantenga el contacto entre la sonda y el metal. Cuando la soldadura tiene un pico demasiado alto, se requiere una técnica diferente que use sonido reflejado para verificar las discontinuidades.
El tamaño de los defectos que se pueden detectar depende de la longitud de onda del sonido. Como regla general, el defecto tiene que ser la mitad de la longitud de onda para ser detectable. Diferentes metales tienen diferentes longitudes de onda para la misma frecuencia de sonido. En acero a 2 MHz, se detectan defectos de 1,5 mm.
Monitoreo de emisiones acústicas
Las emisiones acústicas son ondas de esfuerzo producidas por movimientos repentinos en materiales sometidos a tensión. Cuando un material se coloca bajo carga, se deforma ligeramente. Los movimientos internos producidos por la deformación crean sonidos que viajan a través de la estructura. Estos sonidos se pueden detectar y localizar la fuente del movimiento. Una vez que se encuentra la fuente, se utilizan otras técnicas de END para cuantificar el movimiento y cualquier presencia de discontinuidades.
Este método se utiliza a menudo en estructuras grandes existentes, como tanques y recipientes a presión, ya que es rápido y de bajo costo. Los sensores fijos se encuentran en la estructura y, por lo general, se colocan cada 1 a 6 metros de distancia. La estructura se «carga» de manera ascendente y escalonada y las emisiones acústicas se registran en un monitor de pantalla. La carga se varía o se mantiene constante durante un período de tiempo y los cambios en las emisiones acústicas indican si la estructura continúa moviéndose internamente.
Al tener en cuenta la velocidad del sonido del metal, el punto de emisión se puede localizar mediante triangulación con buena precisión. El ruido de fondo puede interferir con los resultados. Este problema se puede resolver deteniendo el ruido en su origen, filtrándolo utilizando la electrónica del equipo de monitoreo o utilizando una frecuencia de medición diferente a la frecuencia de ruido.
Radiografía industrial
La inspección radiográfica se basa en la absorción de radiación por materiales de diferente densidad. En la industria de la ingeniería se utilizan rayos X o rayos gamma. Es un proceso costoso, pero penetra casi todos los materiales a grandes profundidades.
La fuente de radiación se coloca en un lado de la soldadura que se está probando y la película «fotográfica» de detección se coloca en el otro lado de la soldadura. A medida que la radiación pasa a través de la soldadura, las discontinuidades actúan como reductores de densidad que permiten que pase más radiación a través de ellas. El alto nivel de radiación aparece como un color más oscuro en la película.
Debido a que la imagen creada en la película es una «sombra», puede verse afectada por factores como cambios en el grosor del sujeto, dispersión de la radiación, factores geométricos que influyen en la radiación, posicionamiento de la fuente, tiempos de exposición y calidad de la película.
Mike Sondalini-Ingeniero de Longevidad de equipos