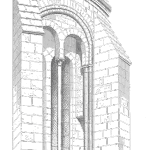
Zerstörungsfreie Prüfung von Schweißnähten. Schweißverfahren und -verfahren können Verunreinigungen und metallurgische Defekte in die Schweißnaht einbringen. Wenn eine Schweißnaht schweren Belastungsbedingungen und Belastungen standhalten muss, ist es wichtig sicherzustellen, dass ihre Qualität den Mindeststandards entspricht. Schweißnähte können zerstörend und zerstörungsfrei geprüft werden. Die meisten Produktionen werden mit zerstörungsfreien Methoden getestet. Die gebräuchlichsten zerstörungsfreien Prüfungen zur Überprüfung von Schweißnähten sind Sichtprüfung, Eindringmittel, Magnetpartikel, Wirbelstrom, Ultraschall, Schallemission und Radiographie. Schlüsselwörter: Zerstörungsfreie Prüfung, Qualitätskontrolle, Nichtkonformität, Überprüfung, Schweißverfahren.
Wenn Metall geschweißt wird, kühlt die geschmolzene Pfütze ab und erstarrt. Während des Abkühlens kann die Schweißnahtqualität durch Einschlüsse wie Schlacke, durch menschliches Versagen aufgrund von Ermüdung, durch falsche Einrichtung und Technik, durch Gerätefehler aufgrund von Ausfällen, durch Umwelteinflüsse wie niedrige Temperatur und Feuchtigkeit und durch metallurgische Phänomene beeinträchtigt werden von inkompatiblen Metallen oder hohen Abkühlraten. Da das Schweißen in hohem Maße von Faktoren abhängt, die vom Menschen kontrolliert werden, muss möglicherweise nachgewiesen werden, dass die Qualität der Arbeit für die Aufgabe geeignet ist.
Bei allen nachfolgend beschriebenen ZFP-Methoden hängt die Sicherheit der Einhaltung vollständig von den Fähigkeiten des Inspektors ab. Qualitativ hochwertige Ergebnisse sind nur von geschulten, kompetenten und erfahrenen Personen möglich. Verwenden Sie keine unqualifizierten Personen, um einen der Tests durchzuführen, von denen Sie gerade lesen werden.
Sichtprüfung
Diese Methode verwendet einen qualifizierten und geschulten Beobachter, der die Schweißnaht während der Arbeit des Schweißers beobachtet. Der Beobachter beobachtet das Schweißbad und das kühlende Metall. Sie suchen typischerweise nach Einschlüssen, Hinterschneidungen (die Schweißnahthöhe liegt unter der Höhe des Grundmetalls), der Eindringtiefe der Schweißnaht und der Sicherheit der Verbindung mit dem Grundmetall.
Wenn ein nicht konformer Defekt festgestellt wird, wird die Stelle markiert. Am Ende des Schweißvorgangs wird der Fehler herausgeschliffen und die Schweißnaht in der erforderlichen Qualität hergestellt.
Flüssigkeits- oder Farbeindringprüfung
Wie der Name schon sagt, wird zur Erkennung von Schweißfehlern ein Farbmittel verwendet. Diese Methode findet nur Oberflächenrisse und Oberflächenkontinuitäten. Die Schweißnahtoberfläche wird gründlich von Zunder und Spritzern gereinigt (jedoch nicht schussgestrahlt, da sie sich über den Defekten schließt). Eine Waschmittelwäsche wird verwendet, um Schmutz zu entfernen, eine Beizpaste wird verwendet, um Farbe oder Fett zu entfernen, und ein Entfetter oder Lösungsmittel wird angewendet, um Öl zu entfernen. Nur eine saubere Metalloberfläche ist akzeptabel.
Das System wird normalerweise in zwei Sprühdosen geliefert – eine ist das Penetrationsmittel und die andere ist der Entwickler. Das Eindringmittel wird über die Schweißnaht gesprüht und durch Kapillarwirkung in winzige Oberflächenrisse gezogen. Das Eindringmittel auf der Oberfläche wird abgewischt und das Eindringmittel in den Rissen bleibt nass. Nach kurzer Verweilzeit wird der Entwickler über die Schweißnaht gesprüht. Der Entwickler zieht den Penetrationsfarbstoff aus den Rissen heraus und ändert so die Farbe. Es verhält sich wie Löschpapier und vergrößert das Vorhandensein des Risses.
Magnetpulverprüfung
Diese Methode verwendet Änderungen in einem Magnetfeld, um Oberflächen- und Knapp unter Oberflächen-Diskontinuitäten zu erkennen. Wenn ein Magnetfeld durch einen Defekt unterbrochen wird, verzerrt sich das Feld um den Defekt herum. Pulverförmige Magnetspäne, die im Feld platziert werden, können diese Verzerrung zeigen. Diese Methode ist nur für ferromagnetische (eisenbasierte magnetische) Metalle verwendbar.
Bei der Prüfung von Schweißnähten wird das Magnetfeld entweder erzeugt, indem Metallstifte auf jeder Seite der Schweißnaht platziert und ein niedriger elektrischer Strom durch das Metall eingeleitet wird, oder indem das Metallteil in ein Magnetfeld gebracht wird. Magnetfelder werden durch das externe Magnetfeld in das Teil induziert.
Sobald das Magnetfeld hergestellt ist, werden einige pulverförmige, farbige Metallpartikel auf das Teil gelegt. Das vom Pulver im Magnetfeld erzeugte Muster wird auf Feldverzerrungen untersucht. Die Partikel können nass (in einer Kerosinsuspension) oder trocken verwendet werden, abhängig von der Position der Teile und dem Zweck der Untersuchung.
Wirbelstromprüfung
Das Funktionsprinzip ist die Erkennung eines veränderten elektrischen Stromflusses in einer Spule aus elektrischem Draht. Der elektrische Wechselstromfluss durch eine Spule erzeugt ein schwankendes Magnetfeld um die Spule herum. Wird das Magnetfeld nahe an leitendes Metall herangeführt, entstehen im Metall elektrische Wirbelströme. Die Wirbelströme wiederum bauen ein Magnetfeld im Gegensatz zum Primärfeld der Spule auf.
Etwaige Schwankungen des sekundären Magnetfeldes aufgrund von Verzerrungen verändern auch die Stärke des Primärfeldes, was wiederum den elektrischen Stromfluss durch die Primärspule verändert. Die Änderung des Primärspulenstromflusses wird erfasst. Der Betrag der Stromänderung stellt den Effekt einer Diskontinuität dar, die die Verzerrung im Sekundärfeld verursacht.
Diese Methode wird verwendet, um Schweißfehler tief im Metall zu erkennen. Tiefen von bis zu 25 mm sind möglich, abhängig vom zu prüfenden Metall und der Geschwindigkeit, mit der sich der Wechselstrom ändert (seine Frequenz).
Dies ist der bevorzugte Ansatz für die Prüfung von Stahlbehälterböden und -wänden. Ein kriechender Scanner wird über die Oberfläche gesendet und Änderungen des Wirbelstroms werden auf einem Überwachungsbildschirm angezeigt. Wenn Beweise für eine Diskontinuität gefunden werden, wird die Stelle markiert und dann eine gründlichere lokale Untersuchung mit anderen ZFP-Geräten durchgeführt, um den Defekt zu quantifizieren.
Ultraschallprüfung
Hochfrequente Schallwellen werden mit einer emittierenden Sonde in ein Metall gesendet. Wenn die Wellen auf eine Diskontinuität stoßen, prallen sie davon ab und kehren zur Sonde zurück, wo sie erkannt werden. Die Größe und Lage der Diskontinuität werden auf einem Überwachungsbildschirm angezeigt.
Die Methode kann nicht für oberflächennahe und oberflächennahe Fehler verwendet werden. Eine Totzone tritt direkt unterhalb des Kontaktpunkts der Sonde auf. Um eine ordnungsgemäße akustische Verbindung zwischen der Sonde und der Metalloberfläche zu gewährleisten, wird ein flüssiges Kupplungsmittel wie Fett zwischen den beiden verwendet. Die Testoberfläche muss glatt genug sein, damit der Haftvermittler den Kontakt zwischen Sonde und Metall aufrechterhalten kann. Wenn die Schweißnaht zu hoch ist, ist eine andere Technik erforderlich, die reflektierten Schall verwendet, um nach Diskontinuitäten zu suchen.
Die Größe der Defekte, die erkannt werden können, hängt von der Wellenlänge des Schalls ab. In der Regel muss der Defekt die halbe Wellenlänge haben, um detektierbar zu sein. Verschiedene Metalle haben unterschiedliche Wellenlängen für die gleiche Schallfrequenz. In Stahl sind bei 2 MHz Defekte von 1,5 mm nachweisbar.
Akustische Emissionsüberwachung
Akustische Emissionen sind Spannungswellen, die durch plötzliche Bewegungen in beanspruchten Materialien erzeugt werden. Wenn ein Material belastet wird, verformt es sich nur geringfügig. Interne Bewegungen, die durch die Verformung erzeugt werden, erzeugen Geräusche, die durch die Struktur wandern. Diese Geräusche können erkannt und die Quelle der Bewegung lokalisiert werden. Sobald die Quelle gefunden ist, werden andere NDT-Techniken verwendet, um die Bewegung und das Vorhandensein von Diskontinuitäten zu quantifizieren.
Diese Methode wird häufig bei vorhandenen großen Strukturen wie Tanks und Druckbehältern verwendet, da sie schnell und kostengünstig ist. Feste Sensoren befinden sich an der Struktur und sind in der Regel alle 1 bis 6 Meter voneinander entfernt. Die Struktur wird schrittweise ansteigend ‚belastet‘ und die akustischen Emissionen auf einem Monitor aufgezeichnet. Die Belastung wird variiert oder für einen bestimmten Zeitraum konstant gehalten und die Änderungen der akustischen Emissionen zeigen an, ob sich die Struktur intern weiter bewegt.
Durch die Berücksichtigung der Schallgeschwindigkeit des Metalls kann der Emissionspunkt durch Triangulation mit guter Genauigkeit lokalisiert werden. Hintergrundgeräusche können die Ergebnisse beeinträchtigen. Dieses Problem kann überwunden werden, indem das Rauschen an seiner Quelle gestoppt wird, indem es mithilfe der Elektronik innerhalb des Überwachungsgeräts herausgefiltert wird oder indem eine andere Messfrequenz als die Rauschfrequenz verwendet wird.
Industrielle Radiographie
Die radiologische Inspektion basiert auf der Absorption von Strahlung durch Materialien unterschiedlicher Dichte. In der Maschinenbauindustrie werden Röntgen- oder Gammastrahlen verwendet. Es ist ein teures Verfahren, das jedoch fast alle Materialien bis in große Tiefen durchdringt.
Die Strahlungsquelle wird auf die eine Seite der zu prüfenden Schweißnaht und der fotografische Nachweisfilm auf die andere Seite der Schweißnaht gelegt. Wenn Strahlung durch die Schweißnaht strömt, wirken Diskontinuitäten als Dichtereduzierer, die mehr Strahlung durch sie hindurch lassen. Die hohe Strahlung zeigt sich als dunklere Farbe auf dem Film.
Da das auf dem Film erzeugte Bild ein ‚Schatten‘ ist, kann es durch Faktoren wie Änderungen der Objektdicke, Strahlungsstreuung, geometrische Faktoren, die die Strahlung beeinflussen, Quellenpositionierung, Belichtungszeiten und Filmqualität beeinflusst werden.
Mike Sondalini – Ingenieur für Langlebigkeit von Geräten