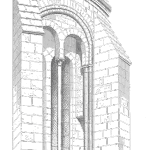
testarea nedistructivă a sudurilor. Procesele și metodele de sudare pot introduce contaminanți și defecte metalurgice în sudură. Dacă este necesară o sudură pentru a rezista la condiții severe de încărcare și solicitări, este esențial să se asigure că calitatea sa respectă standardele minime. Sudurile pot fi testate prin tehnici distructive și nedistructive. Cea mai mare parte a producției este testată prin utilizarea unor metode nedistructive. Cele mai frecvente teste nedistructive pentru verificarea sudurilor sunt inspecția vizuală, Penetrantul lichid, particulele magnetice, curentul turbionar, emisia ultrasonică, acustică și radiografia. Cuvinte-cheie: NDT, controlul calității, neconformitate, verificare, procedură de sudură.
când metalul este sudat, băltoaca topită se răcește și se solidifică. În timpul răcirii, calitatea sudurii poate fi compromisă de incluziuni precum zgura, de eroarea umană cauzată de oboseală, de configurarea și tehnica greșită, de eroarea echipamentului datorată defecțiunilor, de efectele asupra mediului, cum ar fi temperatura scăzută și umiditatea, și de fenomenul metalurgic din metale incompatibile sau rate ridicate de răcire. Deoarece sudarea depinde în mare măsură de factorii controlați de oameni, poate fi necesar să se demonstreze că calitatea lucrării este adecvată pentru datorie.
în toate metodele NDT descrise mai jos, certitudinea conformității depinde în întregime de capacitatea inspectorului. Rezultatele de înaltă calitate sunt posibile numai de la oameni instruiți, competenți și experimentați. Nu folosiți persoane necalificate pentru a face oricare dintre testele pe care urmează să le citiți.
inspecție vizuală
această metodă utilizează un observator calificat și instruit care urmărește sudura în timp ce sudorul funcționează. Observatorul urmărește piscina de sudură și metalul de răcire. De obicei, caută incluziuni, subcotare (înălțimea sudurii este sub înălțimea metalului părinte), adâncimea penetrării sudurii și certitudinea lipirii de metalul părinte.
când se observă un defect de neconformitate, punctul este marcat. La sfârșitul rulării sudurii, defectul este împământat și sudura este refăcută la calitatea necesară.
Inspecția Penetrantului lichid sau colorant
după cum sugerează și numele, un agent colorant este utilizat pentru a detecta defectele de sudură. Această metodă va găsi doar fisuri de suprafață și discontinuități de suprafață. Suprafața de sudură este curățată temeinic de scară și stropi (dar nu împușcat sablat, deoarece se va închide peste defectele). O spălare cu detergent este utilizată pentru a îndepărta murdăria, o pastă de decapare este utilizată pentru a îndepărta vopseaua sau grăsimea și se aplică un degresant sau solvent pentru a îndepărta uleiul. Numai o suprafață metalică curată este acceptabilă.
sistemul vine în mod normal în două cutii de pulverizare – unul este penetrantul și celălalt este dezvoltatorul. Penetrantul este pulverizat peste sudură și acțiunea capilară îl atrage în orice fisuri de suprafață minut. Penetrantul de pe suprafață este șters și penetrantul din fisuri rămâne umed. După o perioadă scurtă de timp, dezvoltatorul este pulverizat peste sudură. Dezvoltatorul acționează pentru a extrage vopseaua penetrantă din fisuri și astfel își schimbă culoarea. Se comportă ca hârtia blotting și mărește prezența fisurii.
Inspecția particulelor magnetice
această metodă utilizează modificări ale unui câmp magnetic pentru a detecta discontinuitățile de suprafață și chiar sub suprafață. Când un câmp magnetic este întrerupt de un defect, câmpul se distorsionează în jurul defectului. Pilitura magnetică sub formă de pulbere plasată în câmp poate arăta această distorsiune. Această metodă este utilizabilă numai pentru metalele Fero-magnetice (magnetice pe bază de fier).
atunci când este utilizat pentru a testa sudurile, câmpul magnetic este produs fie prin plasarea de tije metalice pe fiecare parte a sudurii și introducerea unui curent electric scăzut prin metal, fie prin plasarea părții metalice într-un câmp magnetic. Câmpurile magnetice sunt induse în parte de câmpul magnetic extern.
odată ce câmpul magnetic este stabilit, câteva particule de metal colorate sub formă de pulbere sunt plasate pe piesă. Modelul creat de pulbere în câmpul magnetic este inspectat pentru distorsiuni de câmp. Particulele pot fi utilizate umede (într-o suspensie de kerosen) sau uscate, în funcție de locația pieselor și de scopul examinării.
inspecție curent turbionar
principiul de funcționare este detectarea fluxului de curent electric schimbat într-o bobină de sârmă electrică. Alternarea fluxului de curent electric printr-o bobină creează un câmp magnetic fluctuant în jurul bobinei. Dacă câmpul magnetic este apropiat de conducerea metalului, în metal se dezvoltă curenți electrici turbionari. La rândul lor, curenții turbionari au creat un câmp magnetic în opoziție cu câmpul primar al bobinei.
orice fluctuații ale câmpului magnetic secundar datorate distorsiunilor modifică, de asemenea, puterea câmpului primar, care la rândul său schimbă fluxul de curent electric prin bobina primară. Se detectează modificarea fluxului de curent al bobinei primare. Valoarea modificării curente reprezintă efectul unei discontinuități care provoacă distorsiunea în câmpul secundar.
această metodă este utilizată pentru a detecta defectele de sudură adânc în metal. Adâncimi de până la 25 mm sunt posibile în funcție de metalul testat și de viteza la care se schimbă curentul alternativ (frecvența acestuia).
aceasta este abordarea favorizată pentru testarea pardoselilor și pereților rezervoarelor din oțel. Un scaner cu crawlere este trimis pe suprafață și modificările curentului turbionar sunt afișate pe un ecran de monitorizare. În cazul în care se constată o discontinuitate, locul este marcat și apoi se efectuează o examinare locală mai amănunțită cu alte echipamente NDT pentru a cuantifica defectul.
inspecție cu ultrasunete
undele sonore de înaltă frecvență sunt trimise într-un metal folosind o sondă emițătoare. Dacă undele se confruntă cu o discontinuitate, ele sări de pe ea și se întorc la sonda unde sunt detectate. Dimensiunea și locația discontinuității sunt afișate pe un ecran de monitorizare.
metoda nu poate fi utilizată pentru defecțiuni de suprafață și de suprafață apropiată. O zonă moartă apare chiar sub punctul de contact al sondei. Pentru a asigura o conexiune acustică adecvată între sondă și suprafața metalică, se utilizează un agent de cuplare lichid, cum ar fi grăsimea, între cele două. Suprafața de testare trebuie să fie suficient de netedă pentru ca agentul de cuplare să mențină contactul dintre sondă și metal. În cazul în care sudura este atinsă prea sus, este necesară o tehnică diferită care utilizează sunetul reflectat pentru a verifica discontinuitățile.
dimensiunile defectelor care pot fi detectate depind de lungimea de undă a sunetului. De regulă, defectul trebuie să fie jumătate din lungimea de undă pentru a fi detectabil. Metalele diferite au lungimi de undă diferite pentru aceeași frecvență sonoră. În oțel la 2 MHz, defectele de 1,5 mm sunt detectabile.
monitorizarea emisiilor acustice
emisiile acustice sunt unde de stres produse de mișcarea bruscă a materialelor stresate. Atunci când un material este plasat sub sarcină se deformează vreodată atât de ușor. Mișcările interne produse de deformare creează sunete care călătoresc prin structură. Aceste sunete pot fi detectate și sursa mișcării localizate. Odată găsită sursa, alte tehnici NDT sunt utilizate pentru a cuantifica mișcarea și orice prezență de discontinuități.
această metodă este adesea utilizată pe structurile mari existente, cum ar fi rezervoarele și recipientele sub presiune, deoarece este rapidă și ieftină. Senzorii fixi sunt amplasați pe structură și de obicei plasați la fiecare 1 până la 6 metri distanță. Structura este ‘încărcată’ în creștere, pas cu pas și emisiile acustice înregistrate pe un monitor de afișare. Încărcarea este variată sau menținută constantă pentru o perioadă de timp, iar modificările emisiilor acustice indică dacă structura continuă să se miște intern.
prin factoring-în viteza sunetului metalului, punctul de emisie poate fi localizat prin triangulare cu o precizie bună. Zgomotul de fond poate interfera cu rezultatele. Această problemă poate fi depășită prin oprirea zgomotului la sursă, prin filtrarea acestuia folosind electronica din echipamentul de monitorizare sau prin utilizarea unei frecvențe de măsurare diferite de frecvența zgomotului.
radiografie industrială
inspecția radiografică se bazează pe absorbția radiațiilor de către Materiale de densitate diferită. În industria ingineriei se utilizează raze X sau raze gamma. Este un proces costisitor, dar pătrunde aproape toate materialele la adâncimi mari.
sursa de radiație este plasată pe o parte a sudurii testate, iar filmul fotografic de detectare este plasat pe cealaltă parte a sudurii. Pe măsură ce radiația trece prin discontinuitățile de sudură acționează ca reductoare de densitate care permit mai multă radiație prin ele. Nivelul ridicat de radiații apare ca o culoare mai închisă pe film.
deoarece imaginea creată pe film este o ‘umbră’, aceasta poate fi afectată de factori precum modificări ale grosimii subiectului, împrăștierea radiațiilor, factori geometrici care influențează radiația, poziționarea sursei, timpii de expunere și calitatea filmului.
Mike Sondalini-Inginer De Longevitate A Echipamentelor