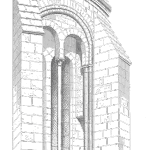
Prova non distruttiva delle saldature. I processi e i metodi di saldatura possono introdurre contaminanti e difetti metallurgici nella saldatura. Se è necessaria una saldatura per resistere a condizioni di carico e sollecitazioni severe, è fondamentale assicurare che la sua qualità soddisfi gli standard minimi. Le saldature possono essere testate con tecniche distruttive e non distruttive. La maggior parte della produzione è testata con l’uso di metodi non distruttivi. Le prove non distruttive più comuni per controllare le saldature sono ispezione visiva, liquido penetrante, particella magnetica, correnti parassite, ultrasuoni, emissione acustica e radiografia. Parole chiave: NDT, controllo qualità, non conformità, verifica, procedura di saldatura.
Quando il metallo è saldato la pozzanghera fusa si raffredda e solidifica. Durante il raffreddamento la qualità della saldatura può essere compromessa da inclusioni come scorie, da errori umani dovuti a fatica, da impostazioni e tecniche errate, da errori di attrezzatura dovuti a guasti, da effetti ambientali come bassa temperatura e umidità e da fenomeni metallurgici derivanti da metalli incompatibili o alti tassi di raffreddamento. Poiché la saldatura dipende fortemente da fattori controllati dall’uomo, forse è necessario dimostrare che la qualità del lavoro è adeguata al dovere.
In tutti i metodi NDT descritti di seguito la certezza della conformità dipende interamente dalla capacità dell’ispettore. I risultati di alta qualità sono possibili solo da persone addestrate, competenti ed esperte. Non utilizzare persone non qualificate per fare uno qualsiasi dei test che si sta per leggere di.
Ispezione visiva
Questo metodo utilizza un osservatore qualificato e addestrato che osserva la saldatura mentre il saldatore sta lavorando. L’osservatore osserva il bagno di saldatura e il metallo di raffreddamento. In genere cercano inclusioni, sottoquotazione (l’altezza della saldatura è inferiore all’altezza del metallo genitore), profondità di penetrazione della saldatura e certezza di legame con il metallo genitore.
Quando si osserva un difetto non conforme, il punto viene contrassegnato. Alla fine della corsa di saldatura il difetto viene rettificato e la saldatura viene rifatta alla qualità richiesta.
Ispezione del liquido o del penetrante della tintura
Come suggerisce il nome un agente colorante è usato per individuare i difetti della saldatura. Questo metodo troverà solo crepe superficiali e discontinuità superficiali. La superficie di saldatura viene accuratamente pulita da incrostazioni e schizzi (ma non sparata in quanto si chiuderà sui difetti). Un lavaggio detergente viene utilizzato per rimuovere lo sporco, una pasta di decapaggio viene utilizzata per rimuovere vernice o grasso e uno sgrassatore o solvente viene applicato per rimuovere l’olio. Solo una superficie metallica pulita è accettabile.
Il sistema viene normalmente fornito in due bombolette spray-uno è il penetrante e l’altro è lo sviluppatore. Il penetrante viene spruzzato sopra la saldatura e l’azione capillare lo attira in qualsiasi minuto crepe superficiali. Il penetrante sulla superficie viene cancellato e il penetrante nelle fessure rimane bagnato. Dopo un breve tempo di sosta lo sviluppatore viene spruzzato sulla saldatura. Lo sviluppatore agisce per estrarre il colorante penetrante dalle fessure e quindi cambia colore. Si comporta come carta assorbente e ingrandisce la presenza della fessura.
Ispezione delle particelle magnetiche
Questo metodo utilizza i cambiamenti in un campo magnetico per rilevare discontinuità superficiali e appena sotto la superficie. Quando un campo magnetico viene interrotto da un difetto, il campo si distorce attorno al difetto. Le limature magnetiche in polvere posizionate sul campo possono mostrare questa distorsione. Questo metodo è utilizzabile solo per metalli ferromagnetici (magnetici a base di ferro).
Quando viene utilizzato per testare le saldature, il campo magnetico viene prodotto posizionando pungoli metallici su ciascun lato della saldatura e introducendo una bassa corrente elettrica attraverso il metallo o posizionando la parte metallica in un campo magnetico. I campi magnetici sono indotti nella parte dal campo magnetico esterno.
Una volta stabilito il campo magnetico, sulla parte vengono poste alcune particelle metalliche colorate in polvere. Il modello creato dalla polvere nel campo magnetico viene ispezionato per le distorsioni del campo. Le particelle possono essere utilizzate a umido (in una sospensione di cherosene) o a secco a seconda della posizione delle parti e dello scopo dell’esame.
Controllo delle correnti parassite
Il principio di funzionamento è la rilevazione del flusso di corrente elettrica modificato in una bobina di filo elettrico. Il flusso di corrente elettrica alternata attraverso una bobina crea un campo magnetico fluttuante attorno alla bobina. Se il campo magnetico viene avvicinato al metallo conduttore, nel metallo si sviluppano correnti elettriche parassite. Le correnti parassite a loro volta impostano un campo magnetico in opposizione al campo primario della bobina.
Eventuali fluttuazioni nel campo magnetico secondario dovute a distorsioni cambiano anche la forza del campo primario, che a sua volta cambia il flusso di corrente elettrica attraverso la bobina primaria. Viene rilevata la variazione del flusso di corrente della bobina primaria. La quantità della variazione corrente rappresenta l’effetto di una discontinuità che causa la distorsione nel campo secondario.
Questo metodo viene utilizzato per rilevare i difetti di saldatura in profondità nel metallo. Profondità fino a 25 mm sono possibili a seconda del metallo testato e della velocità di a cui cambia la corrente alternata (la sua frequenza).
Questo è l’approccio preferito per testare pavimenti e pareti di serbatoi in acciaio. Uno scanner strisciante viene inviato attraverso la superficie e le modifiche nella corrente parassita vengono visualizzate su una schermata di monitoraggio. Quando si riscontra la prova di una discontinuità, il punto viene contrassegnato e quindi viene condotto un esame locale più approfondito con altre apparecchiature NDT per quantificare il difetto.
Ispezione ultrasonica
Le onde sonore ad alta frequenza vengono inviate in un metallo utilizzando una sonda emettitrice. Se le onde incontrano una discontinuità, rimbalzano e ritornano alla sonda dove vengono rilevate. La dimensione e la posizione della discontinuità vengono visualizzate su una schermata di monitoraggio.
Il metodo non può essere utilizzato per difetti superficiali e vicini alla superficie. Una zona morta si verifica appena sotto il punto di contatto della sonda. Per assicurare una corretta connessione acustica tra la sonda e la superficie metallica, viene utilizzato un agente di accoppiamento liquido, come il grasso, tra i due. La superficie della prova deve essere abbastanza regolare affinchè l’agente dell’accoppiamento mantenga il contatto fra la sonda ed il metallo. Dove la saldatura è raggiunto un picco troppo alto è necessaria una tecnica diversa che utilizza il suono riflesso per verificare la presenza di discontinuità.
Le dimensioni dei difetti che possono essere rilevati dipendono dalla lunghezza d’onda del suono. Di norma il difetto deve essere la metà della lunghezza d’onda per essere rilevabile. Metalli diversi hanno lunghezze d’onda diverse per la stessa frequenza sonora. In acciaio a 2 MHz sono rilevabili difetti di 1,5 mm.
Monitoraggio delle emissioni acustiche
Le emissioni acustiche sono onde di stress prodotte da movimenti improvvisi di materiali sollecitati. Quando un materiale viene posto sotto carico, si deforma leggermente. I movimenti interni prodotti dalla deformazione creano suoni che viaggiano attraverso la struttura. Questi suoni possono essere rilevati e la fonte del movimento si trova. Una volta trovata la fonte vengono utilizzate altre tecniche NDT per quantificare il movimento e l’eventuale presenza di discontinuità.
Questo metodo è spesso utilizzato su strutture di grandi dimensioni esistenti, come serbatoi e recipienti a pressione, in quanto è veloce e a basso costo. I sensori fissi si trovano sulla struttura e in genere posizionati ogni 1-6 metri di distanza. La struttura è ‘caricata’ in modo crescente e graduale e le emissioni acustiche registrate su un monitor. Il carico è variato o mantenuto costante per un periodo di tempo e le variazioni delle emissioni acustiche indicano se la struttura continua a muoversi internamente.
Considerando la velocità del suono del metallo, il punto di emissione può essere localizzato mediante triangolazione con una buona precisione. Il rumore di fondo può interferire con i risultati. Questo problema può essere superato arrestando il rumore alla fonte, filtrandolo utilizzando l’elettronica all’interno dell’apparecchiatura di monitoraggio o utilizzando una frequenza di misurazione diversa dalla frequenza del rumore.
Radiografia industriale
L’ispezione radiografica si basa sull’assorbimento delle radiazioni da parte di materiali di diversa densità. Nell’industria ingegneristica vengono utilizzati raggi X o raggi gamma. È un processo costoso ma penetra quasi tutti i materiali a grandi profondità.
La sorgente di radiazione viene posta su un lato della saldatura in fase di test e la pellicola “fotografica” di rilevamento viene posizionata sull’altro lato della saldatura. Come radiazione passa attraverso le discontinuità di saldatura agiscono come riduttori di densità permettendo più radiazione attraverso di loro. L’alto livello di radiazione si presenta come un colore più scuro sulla pellicola.
Poiché l’immagine creata sul film è un’ombra, può essere influenzata da fattori quali cambiamenti nello spessore del soggetto, dispersione delle radiazioni, fattori geometrici che influenzano la radiazione, posizionamento della sorgente, tempi di esposizione e qualità del film.
Mike Sondalini – Equipment Longevity Engineer