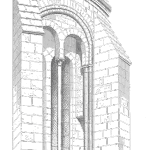
badania nieniszczące spoin. Procesy i metody spawania mogą wprowadzać zanieczyszczenia i wady metalurgiczne do spoiny. Jeśli spoina jest wymagana do wytrzymania ciężkich warunków obciążenia i naprężeń, kluczowe znaczenie ma zapewnienie, że jej jakość spełnia minimalne standardy. Spoiny mogą być testowane za pomocą technik niszczących i nieniszczących. Większość produkcji jest testowana metodami nieniszczącymi. Najczęstsze badania nieniszczące do sprawdzania spoin to kontrola wzrokowa, Penetrant cieczy, cząstki magnetyczne, prąd wirowy, ultradźwięki, emisja akustyczna i radiografia. Słowa kluczowe: badania nieniszczące, kontrola jakości, niezgodność, weryfikacja, procedura spawania.
po spawaniu metalu stopiona kałuża chłodzi się i krzepnie. Podczas chłodzenia jakość spoiny może być zagrożona przez wtrącenia, takie jak żużel, błąd ludzki spowodowany zmęczeniem, Niewłaściwa konfiguracja i technika, błąd sprzętu spowodowany awariami, skutki środowiskowe, takie jak niska temperatura i wilgoć, oraz zjawisko metalurgiczne z niekompatybilnych metali lub wysokie szybkości chłodzenia. Ponieważ spawanie jest w dużym stopniu zależne od czynników kontrolowanych przez ludzi, Być może konieczne jest udowodnienie, że jakość pracy jest odpowiednia do danego zadania.
we wszystkich metodach badań nieniszczących opisanych poniżej pewność zgodności jest całkowicie zależna od zdolności Inspektora. Wysokiej jakości wyniki są możliwe tylko od przeszkolonych, kompetentnych i doświadczonych ludzi. Nie używaj niewykwalifikowanych osób do wykonania żadnego z testów, o których masz zamiar przeczytać.
oględziny
metoda ta wykorzystuje wykwalifikowanego i przeszkolonego obserwatora obserwującego spoinę podczas pracy spawacza. Obserwator obserwuje basen spawalniczy i chłodzący metal. Zazwyczaj szukają wtrąceń, podcięcia (wysokość spoiny jest poniżej wysokości metalu macierzystego), głębokości penetracji spoiny i pewności wiązania z metalem macierzystym.
w przypadku stwierdzenia niezgodności wady punkt jest oznaczony. Na końcu przebiegu spoiny wada jest szlifowana, a spoina jest przekształcana do wymaganej jakości.
Kontrola penetracji cieczy lub barwnika
jak sama nazwa wskazuje, do wykrywania wad spawania stosuje się barwnik. Ta metoda znajdzie tylko pęknięcia powierzchniowe i nieciągłości powierzchni. Powierzchnia spoiny jest dokładnie oczyszczona z kamienia i rozprysków (ale nie śrutowana, ponieważ zamyka się nad wadami). Do usuwania zabrudzeń stosuje się mycie detergentem, do usuwania farby lub tłuszczu stosuje się pastę do wytrawiania, a do usuwania oleju stosuje się odtłuszczacz lub rozpuszczalnik. Dopuszczalna jest tylko czysta metalowa powierzchnia.
system zwykle występuje w dwóch puszkach zraszających-jedna to penetrant, a druga Wywoływacz. Penetrant jest rozpylany na spoinę, a działanie kapilarne wciąga go w wszelkie drobne pęknięcia powierzchni. Penetrant na powierzchni jest wycierany, a penetrant w szczelinach pozostaje mokry. Po krótkim czasie oczekiwania Wywoływacz jest rozpylany na spoinę. Wywoływacz działa w celu wyciągnięcia barwnika penetrantowego z pęknięć i tym samym zmienia kolor. Zachowuje się jak bibułka i powiększa obecność pęknięcia.
Kontrola cząstek magnetycznych
ta metoda wykorzystuje zmiany w polu magnetycznym do wykrywania nieciągłości powierzchni i tuż pod powierzchnią. Gdy pole magnetyczne jest przerwane przez defekt, pole zniekształca się wokół defektu. Sproszkowane opiłki magnetyczne umieszczone w polu mogą pokazać to zniekształcenie. Metoda ta jest użyteczna tylko dla metali żelazomagnetycznych (magnetycznych na bazie żelaza).
w przypadku stosowania do badania spoin pole magnetyczne jest wytwarzane przez umieszczenie metalowych prodów po każdej stronie spoiny i wprowadzenie niskiego prądu elektrycznego przez metal lub przez umieszczenie metalowej części w polu magnetycznym. Pola magnetyczne są indukowane do części przez zewnętrzne pole magnetyczne.
po ustabilizowaniu się pola magnetycznego na części umieszcza się kilka sproszkowanych, kolorowych cząstek metalu. Wzór utworzony przez proszek w polu magnetycznym jest sprawdzany pod kątem zniekształceń pola. Cząstki mogą być używane na mokro (w zawiesinie nafty) lub na sucho, w zależności od lokalizacji części i celu badania.
kontrola prądu wirowego
zasadą działania jest wykrywanie zmienionego przepływu prądu elektrycznego w cewce przewodu elektrycznego. Przemienny przepływ prądu elektrycznego przez cewkę tworzy zmienne pole magnetyczne wokół cewki. Jeśli pole magnetyczne zbliży się do przewodzącego metalu, w metalu rozwijają się wirowe prądy elektryczne. Prądy wirowe z kolei tworzą pole magnetyczne w opozycji do pola pierwotnego cewki.
wszelkie wahania wtórnego pola magnetycznego spowodowane zniekształceniami zmieniają również siłę pola pierwotnego, co z kolei zmienia przepływ prądu elektrycznego przez cewkę pierwotną. Wykryto zmianę przepływu prądu pierwotnego cewki. Wielkość zmiany prądu reprezentuje efekt nieciągłości powodujący zniekształcenia w polu wtórnym.
ta metoda służy do wykrywania defektów spawania głęboko w metalu. Głębokość do 25 mm jest możliwa w zależności od badanego metalu i prędkości, z jaką zmienia się prąd przemienny (jego częstotliwość).
jest to preferowane podejście do testowania stalowych podłóg i ścian zbiorników. Skaner pełzający jest wysyłany po powierzchni, a zmiany w prądzie wirowym są pokazywane na ekranie monitorowania. W przypadku stwierdzenia nieciągłości plamka jest oznaczana, a następnie przeprowadza się dokładniejsze badanie miejscowe przy użyciu innych urządzeń NDT w celu ilościowego określenia wady.
kontrola ultradźwiękowa
fale dźwiękowe o wysokiej częstotliwości są wysyłane do metalu za pomocą sondy emitującej. Jeśli fale napotkają nieciągłość, odbijają się od niej i wracają do sondy, gdzie są wykrywane. Rozmiar i położenie nieciągłości są wyświetlane na ekranie monitorowania.
metoda nie może być stosowana w przypadku usterek powierzchniowych i blisko powierzchniowych. Martwa strefa występuje tuż poniżej punktu styku sondy. Aby zapewnić prawidłowe połączenie akustyczne między sondą a powierzchnią metalu, pomiędzy nimi stosuje się płynny środek sprzęgający, taki jak smar. Powierzchnia badana musi być wystarczająco gładka, aby środek sprzęgający utrzymywał kontakt między sondą a metalem. Tam, gdzie spoina jest zbyt wysoka, wymagana jest inna technika, która wykorzystuje odbity dźwięk, aby sprawdzić nieciągłości.
rozmiary defektów, które można wykryć, zależą od długości fali dźwięku. Z reguły wada musi wynosić połowę długości fali, aby była wykrywalna. Różne metale mają różne długości fal dla tej samej częstotliwości dźwięku. W stali przy częstotliwości 2 MHz wykrywane są defekty 1,5 mm.
monitorowanie emisji akustycznej
emisje akustyczne to fale naprężeń wytwarzane przez nagły ruch materiałów sprężonych. Kiedy materiał jest umieszczany pod obciążeniem, odkształca się nieznacznie. Wewnętrzne ruchy wytwarzane przez deformację tworzą dźwięki, które podróżują przez strukturę. Dźwięki te mogą być wykrywane i źródło ruchu znajduje. Po znalezieniu źródła inne techniki NDT są używane do ilościowego określenia ruchu i jakiejkolwiek obecności nieciągłości.
metoda ta jest często stosowana na istniejących dużych konstrukcjach, takich jak zbiorniki i zbiorniki ciśnieniowe, ponieważ jest szybka i tania. Czujniki stałe znajdują się na konstrukcji i zazwyczaj są umieszczane co 1 do 6 metrów od siebie. Konstrukcja jest „ładowana” w sposób rosnący, stopniowy, a emisja akustyczna rejestrowana jest na monitorze. Obciążenie jest zmienne lub utrzymywane na stałym poziomie przez pewien czas, a zmiany emisji akustycznej wskazują, czy konstrukcja nadal się porusza.
przez uwzględnienie-w prędkości dźwięku metalu, punkt emisji może być zlokalizowany przez triangulację z dobrą dokładnością. Hałas w tle może zakłócać wyniki. Problem ten można przezwyciężyć zatrzymując hałas u źródła, filtrując go za pomocą elektroniki w sprzęcie monitorującym lub stosując inną częstotliwość pomiarową niż częstotliwość szumu.
radiografia przemysłowa
Kontrola radiograficzna opiera się na absorpcji promieniowania przez materiały o różnej gęstości. W przemyśle inżynieryjnym stosuje się promienie rentgenowskie lub gamma. Jest to kosztowny proces, ale penetruje prawie wszystkie materiały na duże głębokości.
źródło promieniowania umieszcza się po jednej stronie badanej spoiny, a wykrywający film „fotograficzny” umieszcza się po drugiej stronie spoiny. Gdy promieniowanie przechodzi przez nieciągłości spoiny działają jako reduktory gęstości, umożliwiając więcej promieniowania przez nie. Wysoki poziom promieniowania objawia się ciemniejszym kolorem na filmie.
ponieważ obraz utworzony na filmie jest „cieniem”, mogą na niego wpływać takie czynniki, jak zmiany grubości obiektu, rozpraszanie promieniowania, czynniki geometryczne wpływające na promieniowanie, położenie źródła, czasy naświetlania i jakość filmu.
Mike Sondalini-Inżynier Sprzętu