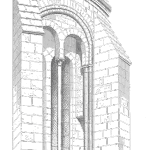
niet-destructief onderzoek van lasnaden. Lasprocessen en-methoden kunnen contaminanten en metallurgische defecten in de las introduceren. Als een Las bestand is tegen zware belastingomstandigheden en spanningen is het van cruciaal belang om te verzekeren dat de kwaliteit ervan voldoet aan minimumnormen. Lassen kunnen worden getest door destructieve en niet-destructieve technieken. De meeste productie wordt getest met behulp van niet-destructieve methoden. De meest voorkomende niet-destructieve tests om lasnaden te controleren zijn visuele inspectie, vloeibare Penetrant, magnetisch deeltje, wervelstroom, Ultrasone, Akoestische emissie en radiografie. Trefwoorden: NDT, kwaliteitscontrole, non-conformiteit, verificatie, lasprocedure.
bij het lassen van metaal koelt en stolt de gesmolten Plas. Tijdens het koelen kan de laskwaliteit worden aangetast door insluitsels zoals slakken, door menselijke fouten als gevolg van vermoeidheid, door verkeerde opstelling en techniek, door apparatuurfouten als gevolg van storingen, door milieueffecten zoals lage temperatuur en vocht, en door metallurgische verschijnselen als onverenigbare metalen of hoge koelsnelheden. Omdat lassen in hoge mate afhankelijk is van door de mens gecontroleerde factoren is het misschien nodig om te bewijzen dat de kwaliteit van het werk geschikt is voor de taak.
bij alle hieronder beschreven NDT-methoden is de zekerheid van naleving volledig afhankelijk van de bekwaamheid van de inspecteur. Resultaten van hoge kwaliteit zijn alleen mogelijk van getrainde, competente en ervaren mensen. Gebruik geen ongekwalificeerde mensen om een van de tests die u op het punt staat te lezen uit te voeren.
visuele controle
bij deze methode wordt gebruik gemaakt van een gekwalificeerde en opgeleide waarnemer die de las bekijkt terwijl de lasser werkt. De waarnemer kijkt naar het lasbad en het koelmetaal. Ze zoeken meestal naar insluitsels, onderbieding (de lashoogte is lager dan de bovenliggende metaalhoogte), diepte van laspenetratie en zekerheid van hechting aan het bovenliggende metaal.
wanneer een defect wordt waargenomen dat niet aan de voorschriften voldoet, wordt de vlek gemarkeerd. Aan het einde van de lasloop wordt het defect weggemalen en wordt de las opnieuw gemaakt tot de vereiste kwaliteit.
vloeistof-of Kleurstofpenetrant controle
zoals de naam al doet vermoeden wordt een kleurstof gebruikt om lasdefecten op te sporen. Deze methode vindt alleen oppervlaktescheuren en oppervlakte-discontinuïteiten. Het lasoppervlak wordt grondig gereinigd van schaal en splatter (maar niet geschoten gestraald als het zal sluiten over de defecten). Een wasmiddel wordt gebruikt om vuil te verwijderen, een beitspasta wordt gebruikt om verf of vet te verwijderen en een ontvetter of oplosmiddel wordt toegepast om olie te verwijderen. Alleen een schoon metalen oppervlak is aanvaardbaar.
het systeem wordt gewoonlijk geleverd in twee spuitbussen – een is de penetrant en de andere is de ontwikkelaar. De penetrant wordt over de las gespoten en capillaire werking trekt het in elke minuut oppervlak scheuren. De penetrant op het oppervlak wordt afgeveegd en de penetrant in de scheuren blijft nat. Na een korte verblijftijd wordt de ontwikkelaar over de las gespoten. De ontwikkelaar handelt om de penetrant kleurstof uit de scheuren te trekken en verandert zo van kleur. Het gedraagt zich als vloeipapier en vergroot de aanwezigheid van de scheur.
magnetische Deeltjesinspectie
deze methode maakt gebruik van veranderingen in een magnetisch veld om oppervlakte-en net onder oppervlakte-discontinuïteiten te detecteren. Wanneer een magnetisch veld wordt onderbroken door een defect, vervormt het veld rond het defect. Gepoederde magnetische vijlsel geplaatst in het veld kan deze vervorming vertonen. Deze methode is alleen bruikbaar voor ferromagnetische (op ijzer gebaseerde magnetische) metalen.
bij gebruik voor het testen van lassen wordt het magnetische veld gevormd door het plaatsen van metalen Prod ‘ s aan elke kant van de las en het introduceren van een lage elektrische stroom door het metaal of door het plaatsen van het metalen deel in een magnetisch veld. Magnetische velden worden in het deel geïnduceerd door het externe magnetische veld.
zodra het magnetisch veld is ingesteld, worden er enkele gepoederde, gekleurde metaaldeeltjes op het deel geplaatst. Het patroon dat door het poeder in het magnetisch veld wordt gecreëerd, wordt gecontroleerd op veldverstoringen. De deeltjes kunnen nat (in een suspensie van kerosine) of droog worden gebruikt, afhankelijk van de plaats van de onderdelen en het doel van het onderzoek.
Wervelstroomcontrole
het werkingsprincipe is het detecteren van veranderde elektrische stroom in een spoel van elektrische draad. Wisselende elektrische stroom door een spoel creëert een fluctuerend magnetisch veld rond de spoel. Als het magnetisch veld dicht bij geleidend metaal wordt gebracht, ontwikkelen zich Elektrische wervelstromen in het metaal. De wervelstromen zetten op hun beurt een magnetisch veld op in tegenstelling tot het primaire veld van de spoel.
fluctuaties in het secundaire magnetische veld als gevolg van vervormingen veranderen ook de sterkte van het primaire veld, die op hun beurt de elektrische stroomstroom door de primaire spoel veranderen. De verandering in de stroom van de primaire spoel wordt gedetecteerd. De hoeveelheid van de huidige verandering vertegenwoordigt het effect van een discontinuïteit die de vervorming in het secundaire veld veroorzaakt.
deze methode wordt gebruikt om lasfouten diep in het metaal op te sporen. Afhankelijk van het te testen metaal en de snelheid waarmee de wisselstroom verandert (de frequentie) zijn diepte tot 25 mm mogelijk.
dit is de voorkeursmethode voor het testen van stalen tankvloeren en-wanden. Een crawling scanner wordt over het oppervlak gestuurd en veranderingen in de wervelstroom worden weergegeven op een monitorscherm. Waar bewijs van een discontinuïteit wordt gevonden, wordt de vlek gemarkeerd en dan wordt een grondiger lokaal onderzoek uitgevoerd met andere NDT-apparatuur om het gebrek te kwantificeren.
Ultrasone inspectie
hoogfrequente geluidsgolven worden in een metaal gestuurd met behulp van een sonde. Als de golven een discontinuïteit tegenkomen, stuiteren ze erop en keren terug naar de sonde waar ze worden gedetecteerd. De grootte en de locatie van de discontinuïteit worden weergegeven op een monitorscherm.
de methode kan niet worden gebruikt voor oppervlaktefouten en nabij-oppervlaktefouten. Een dode zone bevindt zich net onder het contactpunt van de sonde. Om een goede akoestische verbinding tussen de sonde en het metalen oppervlak te verzekeren wordt een vloeibaar koppelmiddel, zoals vet, gebruikt tussen de twee. Het testoppervlak moet glad genoeg zijn om het koppelmiddel in contact te houden tussen de sonde en het metaal. Waar de las te hoog piekt is een andere techniek vereist die gereflecteerd geluid gebruikt om te controleren op discontinuïteiten.
de grootte van de fouten die kunnen worden gedetecteerd, hangt af van de golflengte van het geluid. In de regel moet het defect de helft van de golflengte zijn om op te sporen. Verschillende metalen hebben verschillende golflengten voor dezelfde geluidsfrequentie. In staal met 2 MHz zijn defecten van 1,5 mm detecteerbaar.
akoestische Emissiebewaking
akoestische emissies zijn spanningsgolven die worden geproduceerd door plotselinge bewegingen in gestresste materialen. Wanneer een materiaal onder belasting wordt geplaatst vervormt het enigszins. Interne bewegingen veroorzaakt door de vervorming creëren geluiden die door de structuur reizen. Deze geluiden kunnen worden gedetecteerd en de bron van de beweging gelokaliseerd. Zodra de bron wordt gevonden worden andere NDT-technieken gebruikt om de beweging en om het even welke aanwezigheid van onderbrekingen te kwantificeren.
deze methode wordt vaak gebruikt voor bestaande grote constructies, zoals tanks en drukvaten, omdat ze snel en goedkoop is. Vaste sensoren bevinden zich op de structuur en worden meestal elke 1 tot 6 meter uit elkaar geplaatst. De structuur wordt stapsgewijs ‘geladen’ en de geluidsemissies worden op een displaymonitor geregistreerd. De belasting wordt gevarieerd of gedurende een bepaalde periode constant gehouden en de veranderingen in de geluidsemissies geven aan of de constructie intern blijft bewegen.
door de geluidssnelheid van het metaal te factoreren, kan het emissiepunt met een goede nauwkeurigheid worden gelokaliseerd door middel van triangulatie. Achtergrondruis kan de resultaten verstoren. Dit probleem kan worden opgelost door het geluid aan de bron te stoppen, door het uit te filteren met behulp van de elektronica in de bewakingsapparatuur of door een andere meetfrequentie te gebruiken dan de geluidsfrequentie.
industriële radiografie
Radiografische inspectie is gebaseerd op de absorptie van straling door materialen met verschillende dichtheid. In de technische industrie worden röntgenstralen of gammastralen gebruikt. Het is een duur proces, maar dringt bijna alle materialen tot grote diepten.
de stralingsbron wordt aan één zijde van de te testen las geplaatst en de detecterende “fotografische” film wordt aan de andere zijde van de las geplaatst. Aangezien de straling door de lasdispanningen gaat fungeren als dichtheidsreductoren die meer straling door hen toestaan. Het hoge stralingsniveau verschijnt als een donkere kleur op de film.
omdat het op de film gemaakte beeld een “schaduw” is, kan het worden beïnvloed door factoren zoals veranderingen in de dikte van de proefpersoon, stralingsverstrooiing, geometrische factoren die de straling beïnvloeden, de plaats van de bron, de belichtingstijden en de filmkwaliteit.
Mike Sondalini-Equipment Longlevity Engineer