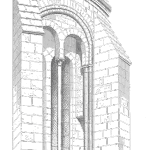
溶接部の非破壊試験。 溶接プロセスおよび方法は溶接に汚染物および冶金の欠陥をもたらすことができます。 溶接が厳しい負荷条件および圧力に抗するように要求されれば質が最低基準に合うことを保証することは重大である。 溶接部は、破壊的および非破壊的な技術によって試験することができる。 ほとんどの生産は非破壊的な方法の使用によってテストされます。 溶接を点検する共通の非破壊的なテストは目視検差、液体の浸透剤、磁気粒子、渦電流、超音波の、音響の放出およびレントゲン写真術です。 キーワード:NDT、品質管理、不適合、検証、溶接手順。
金属を溶接すると、溶融した水たまりが冷やされて凝固します。 冷却の間に溶接質はスラグのような包含によって、疲労からの人的ミスによって、間違った組み立ておよび技術によって、故障による装置の間違いによ 溶接は人間によって制御される要因に大きく依存しているので、仕事の質が義務のために適切であることを証明することが必要かもしれません。
以下に記載されているすべてのNDT方法において、コンプライアンスの確実性は検査官の能力に完全に依存しています。 高品質の結果は、訓練された有能で経験豊富な人々からのみ可能です。 あなたが読むことを約あるテストの何れかをするのに修飾されていない人々を使用してはいけない。
目視検査
この方法は、溶接機が動作しているときに溶接を見て資格と訓練を受けた観察者を使用しています。 観察者は溶接プールおよび冷却の金属を見る。 それらは普通包含、アンダーカット(溶接高さは親金属の高さの下にあります)、溶接浸透の深さおよび親金属への結合の確実性を捜します。
準拠していない欠陥が観察された場合、スポットがマークされます。 溶接操業の終わりに欠陥はひかれ、溶接は必須の質に作り直されます。
液体または染料浸透検査
名前が示すように、着色剤が溶接欠陥を検出するために使用されます。 この方法では、表面の亀裂と表面の不連続性のみが検出されます。 溶接表面はスケールおよびスプラッターの完全にきれいになります(しかし欠陥に閉まると同時に発破を掛けられて撃たれません)。 洗剤洗浄は汚れを除去するために使用され、酸洗ペーストは塗料またはグリースを除去するために使用され、脱脂剤または溶剤は油を除去するために きれいな金属表面だけ受諾可能です。
システムは通常、二つのスプレー缶に入っています–一つは浸透剤であり、もう一つは現像剤です。 浸透剤は溶接に吹きかかり、毛細管現象はあらゆる微細な表面のひびにそれを引く。 表面の浸透剤は拭かれ、ひびの浸透剤はぬれた残ります。 短い滞留時間の後で開発者は溶接に吹きかかる。 現像剤は、浸透性染料を亀裂から引き出し、色を変化させるように作用する。 それは紙をしみのように振る舞い、亀裂の存在を拡大する。
磁性粒子検査
この方法は、磁場の変化を使用して表面および表面のすぐ下の不連続性を検出します。 磁場が欠陥によって中断されると、磁場は欠陥の周りを歪ませる。 フィールドに配置された粉末状の磁気ファイリングは、この歪みを示すことができます。 この方法は、強磁性(鉄系磁性)金属にのみ使用可能です。
溶接のテストに使用する場合、磁場は、溶接の両側に金属プロッドを配置し、金属に低電流を導入するか、金属部品を磁場に配置することによって生成 外部磁場によって部品に磁場が誘起されます。
磁場が確立されると、いくつかの粉末化された着色された金属粒子が部品上に配置されます。 磁場中の粉末によって作成されたパターンは、磁場の歪みのために検査される。 粒子は、部品の場所や検査の目的に応じて、湿式(灯油の懸濁液中)または乾式で使用することができます。
渦電流検査
動作原理は、電線のコイル内の変化した電流の流れを検出することです。 コイルを通る交流電流の流れはコイルのまわりで変動の磁界を作成します。 磁場が導電性金属に近づくと、金属内に渦電流が発生します。 渦電流は、コイルの一次磁場に反対して磁場を設定します。
歪みによる二次磁場の変動も一次磁場の強さを変化させ、一次コイルを流れる電流を変化させる。 一次コイル電流の流れの変化を検出する。 電流変化の量は、二次電界の歪みの原因となる不連続の影響を表します。
この方法は、金属の深部にある溶接欠陥を検出するために使用されます。 25までのmmの深さはテストされる金属および交流が変わる速度によって可能である(頻度)。
これは鋼製タンクの床と壁をテストするための好ましいアプローチです。 クロールスキャナが表面を横切って送信され、渦電流の変化が監視画面に表示されます。 不連続の証拠が見つけられるところで点は印が付き、次に欠陥を量を示すために他のNDT装置によってより完全なローカル検査は行なわれます。
超音波検査
高周波音波を発光プローブを使用して金属に送ります。 波が不連続に遭遇した場合、それらはそれを跳ね返り、それらが検出されたプローブに戻る。 不連続のサイズそして位置は監視スクリーンに表示される。
この方法は、表面および表面近傍の断層には使用できません。 デッドゾーンは、プローブの接触点のすぐ下に発生します。 プローブと金属表面との間の適切な音響接続を保証するために、グリースのような液体カップリング剤が両者の間に使用される。 テスト表面はカップリングの代理店が調査と金属間の接触を維持することができるように十分に滑らかであるように要求されます。 溶接が余りに高く最高になるところで不連続があるように確認するのに反射音を使用する別の技術は要求される。
検出できる欠陥の大きさは、音の波長によって異なります。 原則として、欠陥は検出可能な波長の半分でなければならない。 異なった金属に同じ健全な頻度のための異なった波長があります。 2MHzの鋼では、1.5mmの欠陥が検出可能です。
音響エミッションモニタリング
音響エミッションは、応力を受けた材料の突然の動きによって生じる応力波です。 材料が負荷の下に置かれるときそうわずかに変形する。 変形によって生成された内部の動きは、構造を移動する音を作成します。 これらの音が検出され、動きの源が位置することができる。 ソースが発見されると、他のNDT技術を使用して、動きおよび不連続の存在を定量化します。
この方法は、高速かつ低コストであるため、タンクや圧力容器などの既存の大型構造物によく使用されます。 固定センサーは構造にあり、普通1から6メートル毎に離れて置かれる。 構造は表示モニターで記録される上昇、段階的な方法および音響の放出で”荷を積まれる”。 荷重は一定の期間変化または保持され、音響放射の変化は、構造が内部的に移動し続けているかどうかを示します。
-金属の音速を因数分解することにより、良好な精度で三角測量によって放出点を見つけることができます。 背景ノイズは結果に干渉する可能性があります。 この問題は、ノイズ源でノイズを停止するか、監視装置内の電子機器を使用してノイズをフィルタリングするか、ノイズ周波数とは異なる測定周波数を
産業用放射線撮影
放射線検査は、異なる密度の材料による放射線の吸収に基づいています。 エンジニアリング業界では、X線またはガンマ線が使用されています。 それは高いプロセスであるが、大きい深さにほとんどすべての材料を突き通す。
放射線源は試験される溶接部の片側に置かれ、検出”写真”フィルムは溶接部の反対側に置かれる。 放射が溶接不連続を通ると同時に密度の減力剤として機能しそれらを通ってより多くの放射を許可する。 放射線の高レベルは、フィルム上の暗い色として表示されます。
フィルム上に作成された画像は”影”であるため、被写体の厚さの変化、放射線の散乱、放射線に影響を与える幾何学的要因、光源の位置、露光時間、フィルムの品質などの要因によって影響される可能性があります。
マイク-ソンダリーニ-機器長寿エンジニア