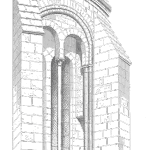
Non-destructive testing of hits. Hitsausprosessit ja-menetelmät voivat tuoda epäpuhtauksia ja metallurgisia vikoja hitsaukseen. Jos hitsin on kestettävä vakavia kuormitusolosuhteita ja korostaa on tärkeää varmistaa sen laatu täyttää vähimmäisvaatimukset. Hitsauksia voidaan testata tuhoavilla ja tuhoamattomilla tekniikoilla. Suurin osa tuotannosta testataan tuhoamattomilla menetelmillä. Yleisimpiä tuhoamattomia testejä hitsien tarkastamiseksi ovat silmämääräinen tarkastus, Nestepenetraatio, Magneettihiukkanen, pyörrevirta, ultraääni, Akustinen emissio ja radiografia. Asiasanat: NDT, laadunvalvonta, vaatimustenvastaisuus, verifiointi, hitsausmenettely.
metallia hitsattaessa sula lätäkkö jäähtyy ja jähmettyy. Jäähdytyksen aikana hitsin laatu voi vaarantua sulkeumat, kuten kuona, inhimillinen virhe väsymys, väärä asennus ja tekniikka, laitevirhe johtuu hajoamista, ympäristövaikutukset, kuten alhainen lämpötila ja kosteus, ja metallurginen ilmiö yhteensopimattomien metallien tai korkea jäähdytysnopeudet. Koska hitsaus on hyvin riippuvainen ihmisen kontrolloimista tekijöistä, on ehkä tarpeen todistaa työn laatu sopivaksi tehtävään.
kaikissa jäljempänä kuvatuissa NDT-menetelmissä vaatimustenmukaisuuden varmuus riippuu täysin tarkastajan kyvystä. Laadukkaat tulokset ovat mahdollisia vain koulutetuilta, osaavilta ja kokeneilta ihmisiltä. Älä käytä epäpäteviä ihmisiä tekemään mitään niistä kokeista, joista olet lukemassa.
silmämääräinen tarkastus
tässä menetelmässä pätevä ja koulutettu tarkkailija tarkkailee hitsausta hitsaajan työskennellessä. Tarkkailija tarkkailee hitsausallasta ja jäähdytysmetallia. Ne etsivät tyypillisesti sulkeumia, alittavuutta (hitsin korkeus on kantametallin korkeuden alapuolella), hitsin tunkeutumisen syvyyttä ja varmuutta sitoutumisesta kantametalliin.
kun havaitaan vaatimustenvastainen vika, piste merkitään. Hitsausajon lopussa vika jauhetaan pois ja hitsaus uusitaan vaadittuun laatuun.
neste-tai Väriainetarkastus
nimensä mukaisesti hitsausvirheiden havaitsemiseen käytetään väriainetta. Tämä menetelmä löytää vain pinnan halkeamia ja pinnan epäjatkuvuutta. Hitsauspinta puhdistetaan perusteellisesti mittakaavasta ja roiskeista (mutta ei räjäytetä, koska se sulkeutuu vikojen yli). Lian poistamiseen käytetään pesuainepesua, maalin tai rasvan poistamiseen peittaustahnaa ja öljyn poistamiseen käytetään rasvanpoistoainetta tai liuotinta. Vain puhdas metallipinta on hyväksyttävä.
järjestelmä tulee normaalisti kahdessa spraypurkissa – toinen on läpivienti ja toinen kehittäjä. Lävistäjä suihkutetaan hitsin päälle ja kapillaari toiminta vetää sen tahansa minuutin pinnan halkeamia. Pinnalla oleva penetrantti pyyhitään pois ja halkeamissa oleva penetrantti pysyy märkänä. Lyhyen viipymisajan jälkeen Kehittäjä ruiskutetaan hitsin päälle. Kehittäjä toimii vetää penetrant väriaine halkeamista ja niin muuttaa väriä. Se käyttäytyy kuin blottaisi paperia ja suurentaa halkeaman läsnäoloa.
Magneettihiukkasten tarkastus
tässä menetelmässä käytetään magneettikentän muutoksia pinnan ja juuri pinnan alla olevien epäjatkuvuuksien havaitsemiseen. Kun magneettikenttä keskeytyy vian vuoksi, kenttä vääristyy vian ympärillä. Kenttään sijoitetut jauhetut magneettiset viilaukset voivat osoittaa tämän vääristymän. Tätä menetelmää voidaan käyttää vain ferromagneettisille (rautapohjaisille) metalleille.
hitsien testauksessa magneettikenttä saadaan aikaan joko sijoittamalla metallitangot hitsin kummallekin puolelle ja tuomalla pieni sähkövirta metallin läpi tai asettamalla metalliosa magneettikenttään. Magneettikentät indusoituvat osaan ulkoisen magneettikentän vaikutuksesta.
magneettikentän muodostuttua osaan asetetaan muutama jauhemainen, värillinen metallihiukkanen. Magneettikentässä olevan jauheen aiheuttama kuvio tutkitaan kenttävääristymien varalta. Hiukkasia voidaan käyttää märkinä (kerosiinisuspensiossa) tai kuivina riippuen osien sijainnista ja tutkimuksen tarkoituksesta.
pyörrevirran tarkastus
toimintaperiaate on muuttuneen sähkövirran havaitseminen sähköjohdon kelassa. Käämin läpi kulkeva vaihtosähkövirta luo kelan ympärille vaihtelevan magneettikentän. Jos magneettikenttä tuodaan lähelle johtavaa metallia, metalliin kehittyy pyörremäisiä sähkövirtoja. Pyörrevirrat puolestaan käynnistivät magneettikentän vastakohtana Kelan primaarikentälle.
mahdolliset vääristymistä johtuvat toisiomagneettikentän vaihtelut muuttavat myös primäärikentän voimakkuutta, mikä puolestaan muuttaa ensiökäämin läpi kulkevaa sähkövirtaa. Ensiökäämivirtauksen muutos havaitaan. Nykyisen muutoksen määrä kuvaa toisiokentän vääristymän aiheuttavan epäjatkuvuuden vaikutusta.
tätä menetelmää käytetään syvällä metallissa olevien hitsausvirheiden havaitsemiseen. Jopa 25 mm: n syvyydet ovat mahdollisia testattavan metallin ja vaihtovirran vaihtumisnopeuden (taajuuden) mukaan.
tämä on ensisijainen lähestymistapa terästankkien lattioiden ja seinien testaamiseen. Ryömivä skanneri lähetetään pinnan yli ja pyörrevirran muutokset näkyvät seurantaruudulla. Jos havaitaan merkkejä epäjatkuvuudesta, piste merkitään, minkä jälkeen tehdään perusteellisempi paikallinen tutkimus muilla NDT-laitteilla virheen määrittämiseksi.
ultraäänitarkastus
korkeataajuiset ääniaallot lähetetään metalliin säteilyanturilla. Jos aallot kohtaavat epäjatkuvuuden, ne kimpoavat siitä ja palaavat luotaimeen, jossa ne havaitaan. Epäjatkuvuuden koko ja sijainti näkyvät seurantanäytöllä.
menetelmää ei voida käyttää pinta-ja lähipinnan virheisiin. Aivan luotaimen kosketuspisteen alapuolella on dead-zone. Oikean akustisen yhteyden varmistamiseksi anturin ja metallipinnan välillä käytetään nestekytkentäainetta, kuten rasvaa, näiden kahden välillä. Testipinnan on oltava riittävän sileä, jotta kytkentäaine voi säilyttää kosketuksen anturin ja metallin välillä. Jos hitsaus on huipussaan liian korkea, tarvitaan erilainen tekniikka, joka käyttää heijastunutta ääntä epäjatkuvuuksien tarkistamiseen.
havaittavien vikojen koot riippuvat äänen aallonpituudesta. Yleensä vian on oltava puolet aallonpituudesta, jotta se voidaan havaita. Eri metalleilla on eri aallonpituudet samalle äänitaajuudelle. 2 MHz: n teräksessä on havaittavissa 1,5 mm: n vikoja.
akustisten päästöjen tarkkailu
akustiset päästöt ovat stressiaaltoja, jotka syntyvät stressaantuneiden materiaalien äkillisestä liikkeestä. Kun materiaali asetetaan kuormaan, se muuttuu hyvin vähän. Muodonmuutoksen tuottamat sisäiset liikkeet luovat ääniä, jotka kulkevat rakenteen läpi. Nämä äänet voidaan havaita ja liikkeen lähde paikantaa. Kun lähde on löydetty, käytetään muita NDT-tekniikoita liikkeen ja epäjatkuvuuden kvantifioimiseen.
tätä menetelmää käytetään usein olemassa olevissa suurissa rakenteissa, kuten säiliöissä ja paineastioissa, koska se on nopea ja edullinen. Kiinteät anturit sijaitsevat rakenteessa ja sijoitetaan tyypillisesti 1-6 metrin välein. Rakenne on ”ladattu” nousevaan, vaiheittaiseen tyyliin ja näyttömonitorin tallentamat akustiset päästöt. Kuormitus vaihtelee tai pysyy vakiona jonkin aikaa, ja akustisten päästöjen muutokset osoittavat, jatkuuko rakenne sisäisesti.
faktoroimalla-metallin äänennopeudessa emissiopiste voidaan paikantaa triangulaatiolla hyvällä tarkkuudella. Taustamelu voi häiritä tuloksia. Tämä ongelma voidaan ratkaista pysäyttämällä melu sen lähteellä, suodattamalla se pois valvontalaitteen elektroniikan avulla tai käyttämällä eri mittaustaajuutta kuin melutaajuus.
Teollisuusradiografia
röntgentutkimus perustuu säteilyn absorptioon eritiheyksisistä materiaaleista. Konepajateollisuudessa käytetään röntgen – tai gammasäteitä. Se on kallis prosessi, mutta läpäisee lähes kaikki materiaalit hyvin syvälle.
säteilylähde asetetaan testattavan hitsin toiselle puolelle ja havaitseva ”valokuvausfilmi” hitsauksen toiselle puolelle. Säteilyn kulkiessa hitsin läpi epäjatkuvuudet toimivat tiheyden vähentäjinä sallien enemmän säteilyä niiden läpi. Suuri säteilytaso näkyy kalvossa tummempana värinä.
koska filmille luotu kuva on ”varjo”, siihen voivat vaikuttaa esimerkiksi kohteen paksuuden muutokset, säteilyn hajaantuminen, säteilyyn vaikuttavat geometriset tekijät, lähteen sijainti, valotusajat ja filmin laatu.
Mike Sondalini-Laitteiden Pitkäikäisyys Insinööri